Grain Quality Tip of the Month
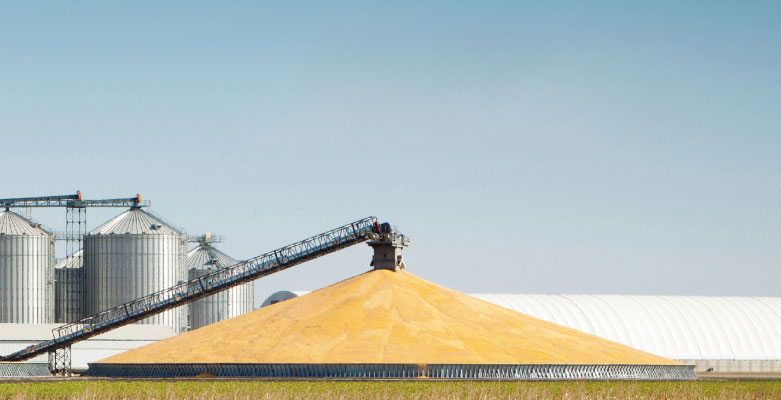
Extron Company stands behind the Aeration and Temperature Monitoring recommendations and tips featured in the recent Grain Journal Enewsletter. Accurate Aeration and Temperature Monitoring in and around grain piles is critical for detecting spoilage and understanding trends. Extron Company provides real-time wireless grain temperatures and CO2 levels. Our system also incorporates VFDs that control and monitor differential pressure, RPM, watts, current, power loss, wind speeds and much more. To learn more about protecting and preserving the health of your harvest, contact an experienced Extron Company Account Manager today!
Aeration and Temperature Monitoring
Grain Journal, August 2017
“Across much of the Midwest, early August tends to be the time of year when many facility operators are getting ready for the upcoming soybean and corn harvests.
Aeration and temperature monitoring are major tools at your disposal to manage Grain Quality.
Here are some tips I hope you find useful:
Aeration Systems
• Check all ductwork for cracks and or loose connections. Expansion joints should be inspected to ensure they are airtight. Even small holes can have a major impact on fan performance.
• Inspect ductwork for buildup of fines and other materials and clean. This is critical, not only for airflow, but leaving that material invites insects, rodents, etc., that you don’t want or need.
• Inspect all vents and exhausters safely, looking for cracks that could allow water into the grain space. On updraft systems, inspect and clean the screen mesh installed to keep critters out, at either the top or bottom of the system.
- If you have power exhausters, make sure they are operating properly.
- This may not seem necessary, but make sure the fans are rotating the correct direction. I’ve seen many cases where a fan or motor was replaced, and the direction was wrong. It will move air, just not as designed. This happens easily on vane axial fans used on many temporary storage systems. They usually have a direction arrow for air flow, and another direction arrow for fan rotation. Make sure both are correct.
- Lastly, check the perforated ductwork/sheeting of your system. Over time, these can become clogged with rust, dust, etc., and the performance of your system will suffer greatly. I would suggest using corn cob grit with a sand blaster pot to lean the ductwork. This solution is simple, effective, and biodegradable. I used it many times in my career and it works perfectly.
Temperature Monitoring
- Check your temperature cables for proper calibration. This can be accomplished when the bin is empty. I’d suggest early in the morning before temperatures increase, as the numbers should be close to ambient from top to bottom. If not, that may indicate a bad cable.
- This is a great time to note what cables might not be operating or are missing. If you can’t replace them before the bin is refilled, record which ones need replaced with an accurate diagram of the cable layout.
- Check with your bin manufacturer, but my experience says the cables should be tied down to the floor to keep when in place and close to vertical during the filling stage. There are several methods that can be used, but I found using a light-duty type of material, like baler twine or electricians’ pulling twine is effective to hold the cable in position. I would not use anything metallic, because if it breaks loose, you could add to your troubles.
Also, if you have a sweep system, the twine will break free easily when needed. From my experience, I would not tie the cables to each other at the bottom, but rather each cable individually tied down separately.
• Lastly, a quick review temperature cable readings from when grain was last in the bin may help identify problematic cables that may show a grain level when the bin is empty.”